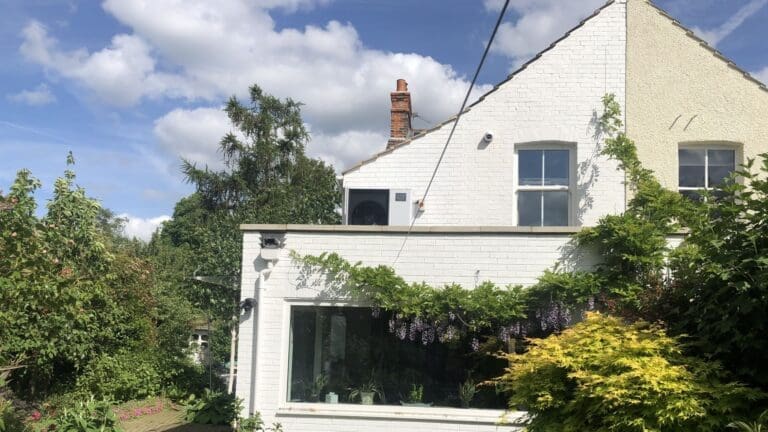
Judith Leary-Joyce went on a huge learning journey during her own home retrofit project and has now written a book to help others get ahead on the road to a more energy-efficient home.
This article has been written based on an interview with Judith and excerpts from her book, the Beginner’s Guide to Eco Renovation.
“Retrofit is to building what Spanx is to a little black dress. If you’ve got the underpinnings right, it’s fabulous, yet no-one really wants to know much about the underpinnings.”
It’s an interesting analogy presented by 75-year-old grandma, Judith Leary-Joyce, who has become affectionately known as the ‘Queen of Insulation’ in her hometown of St Albans.
When Judith embarked on a huge retrofit project of her leaky and cold Victorian terrace four years ago, little did she know it would lead to her writing a book, giving a Tedx Talk, and becoming a social media sensation, racking up an incredible 60,000 followers and 19 million views on Instagram.
A self-confessed ‘eco-worrier’, Judith has been championing the climate since the 1970s, having joined Friends of the Earth when it was first formed. She’s studied deep ecology, marched for the environment, shaken tins to raise funds, ditched plastic where possible and eats vegan food.
So when Judith and husband John (70) decided to rip down their draughty too hot, too cold conservatory and replace it with a new rear extension, it was only ever going to be an eco-friendly build.
The extension
The starting point for the extension which is 7.5 x 2.2 metres (internal measurements) was an air source heat pump (ASHP). John had been watching their progress for a long time and knew he wanted one.
Their architect advised that good insulation was key to support the ASHP and recommended using a breathable membrane across the walls, building a stud frame to hold the insulation, putting 80mm of wood fibre insulation batts (Pavaflex) into each gap in the framework and covering this with rigid 40mm boards of Isolair – the wood equivalent of plasterboard.
But it wasn’t long before the big realisation came; however well the extension was prepared for the ASHP, the heat would quickly be lost through the rest of the leaky old end-terrace.
The couple decided they would have to retrofit their way back through the entire house, although at that point, they didn’t even know it was called retrofitting.
The retrofit
Judith threw herself into the project from day one.
“I was hooked straight away,” Judith said. “I was up until 2am researching that very first day. I was grappling with dense and convoluted information, talking to experts about topics I didn’t even know existed, but back then, we didn’t know what we didn’t know.
“It was the day I discovered the word ‘retrofit’ though, as opposed to renovation, that everything changed.”
One of the main points of learning was about how ‘the big four’ – insulation, air tightness, ventilation and breathability – all work together, and this became the foundation of the retrofit project.
“If you insulate without airtightness, you’ll be disappointed. Insulation won’t stop the draughts so you’ll still feel chilly. If you insulate and get airtight, but don’t ventilate, the air will feel stale and you’ll invite condensation and maybe mould.
“If you live in an old house, leaving breathability out of the equation will also promote condensation and mould.”
So while in some respects they were able to carry on as they’d started in the extension, there were many elements of the old building that required a more creative approach.
Insulation
This became something of an obsession for Judith as the first piece in the ‘big four’ puzzle. Yet in a solid-wall Victorian property with one big unprotected wall, this was no mean feat. As well as single brick walls, there were suspended timber floors, single glazed windows and large chimney shafts to contend with.
Just as with the extension, Judith and John preferred not to use the most common insulation, PIR, because it’s made from petrochemical substances, releases emissions during production and creates hazardous waste at the end of its life.
While they had to use it in a couple of areas, they opted in the main for the wood fibre insulation approach which they’d used in the extension.
Wood fibre is robust, flexible and recyclable. It comes in soft batts and can be tightly packed into floors, roofs and walls.
They did some of this work themselves and became adept at putting the jigsaw together, leaving no gap unstuffed.
Particular attention was paid to thermal bridges – areas that conduct heat more easily than surrounding materials – and U values which indicate how effective insulation will be based on heat lost.
There was one area which didn’t allow for the wood frame insulation system – the Victorian bay window. It remained a challenge for a long time, until Judith found an environmental architect who told her about Diathonite – a thermal plaster which can be used on corners and angles.
The old lime plaster first had to be removed to bare brick and a deeper frame built to accommodate the increased wall depth. Specialist plasterers trowelled the Diathonite on in three layers.
In the loft, 100mm thickness of sheep’s wool was used with wooden board underneath to allow for storage, with 50mm of Pavatherm and 40mm of Isolair between and below the rafters.
After the house had been packed as tight as possible, Judith and John even went to the trouble of borrowing a thermal imaging camera from the council to check their handiwork. As well as highlighting cold spots, they used the images to show the window installers cold gaps between the door frame and the wall. They were then able to identify and rectify a faulty latch that had pinged off the sash.
Airtightness
Drafts can quickly leak away 20% of heat generated – something Judith was keen to avoid. In a new build, this can be prevented with a vapour control membrane, but going back through an old house is much more challenging.
It meant forensically examining every nook and cranny for gaps, such as around utility pipes, and holes in the fabric, chimneys, fireplaces, walls and doors. Then sealing them up with insulation (in big spaces such as under the sink and kitchen cupboards), tape (for example sealing gaps between the walls and floor) and expandable foam (as an environmental last resort).
Triple-glazed windows and doors were chosen, which have to be fitted properly to achieve maximum airtightness.
Judith shares an example, in her book, of how a mistake in the fitting of the windows jeopardised airtightness.
As for the chimneys, they took one out altogether. While this was one major source of draught gone for good, another was kept as the couple love a fire, but it remains something they are grappling with.
Same as with the insulation, Judith and John checked their work with an airtightness test, which basically involves putting a huge fan in a doorway to suck air in to reveal any holes or gaps.
“This was such an eye opener, I’m so pleased we did it,” said Judith. “We found drafts all over the place that we didn’t know about. Even where the original sash windows had been refurbished there was air coming up through the rope hole.
“We also needed to seal between the front room floorboards. In fact, we put an additional airtight membrane over the floor to make sure we’d caught them all.”
Breathability
The breathability part of the equation meant dealing with moisture in the air caused by both internal and external sources. When any warm air lands on a cold surface, it condenses, risking damp and mould. In her book, Judith includes the statistic that the average family can produce up to 15 litres of water vapour in one day just through normal activities.
Yet with all that work done to make the house airtight, there’s no easy escape for moisture-laden air.
Old houses are more breathable by design due to the use of materials such as stone, brick and earth or lime-based mortars, combined with a lack of airtightness. But once you try to make them more efficient, moisture becomes an issue.
As wood fibre is a breathable material, it needed to be covered with lime plaster, which is also breathable. While Judith found it tricky to find a lime plasterer, techniques have already moved on to make this process easier now.
It was all finished off with breathable paint.
Ventilation
The house is warm and well insulated, it’s breathable and all gaps are removed. But now the air flow is removed and there’s the water vapour to manage. Judith and John wanted to take control of the air circulation in their home.
They opted for six single-room heat recovery ventilation fans which consistently move air in and out of rooms. They’re left on 24/7and have variable speeds that change according to the humidity. The heat recovery option means up to 95% of the heat in a room is passed from the outgoing warm air pipe to the incoming cold air pipe to bring warm, fresh air into a room.
Judith writes: “It was one of those fortuitous internet searches. We knew we needed ventilation and we knew about mechanical ventilation heat recovery. It sounded fantastic, but there was no way it would fit into our old house. So I had to get on the case and find something that would work. Eventually I came across a single-room heat recovery extractor fan. It was so exciting!”
They opted for Envirovents with a Blauberg in the bathroom which has an adjustable humidity sensor.
The renewables
The air source heat pump was the catalyst for the entire project. Judith and John chose the Mitsubishi 8.5kWh heat pump which is mounted on the flat roof of the new extension.
Despite being initially concerned about noise, Judith says other than a ‘gentle thrum’ on bitterly cold days, she mostly doesn’t notice it all, whether inside or outside.
The heat pump has been paired with a combination of radiators and underfloor heating. Underfloor heating in the dining room and kitchen/family room where there’s wooden flooring, and radiators in the front room and upstairs where there’s carpet.
Because they were concerned whether they would be warm enough, they chose larger radiators and kept an existing radiator in the dining room in addition to the underfloor heating.
Now with the benefit of hindsight, they feel this was probably ‘overkill’ as they only use one of the radiators and only intermittently.
To maximise their power generation, Judith and John paired their heat pump with solar panels. Not blessed with a south-facing roof, they have five panels facing east and three facing west. The 10 JA Solar 440 mono / all black panels fitted with a GivEnergy 3.6kW hybrid inverter achieve around 75% of an average south-facing output.
The result
The Leary-Joyces have reduced their annual energy consumption, and their bills, by an impressive 75%, down from 25,500 KWh per year to less than 6000.
Their house has been valued at an additional £90,000 and upgraded from an energy performance certificate rating D to B.
The couple are more comfortable, considerably warmer, and feeling incredibly happy about the legacy they are leaving.
“We need to accept that our homes are part of the problem. This is one piece of climate action that has no sacrifice, you can only win. Around 21% of UK emissions come from leaky homes, so if everyone could get working on their houses, whether a deep or shallow retrofit, we could make a big dent in those emissions.”
The part the installer can play
Judith said: “Conversations with builders are generally top down. They tell you what you need and we go along with it because we want the difficult bit to be over.
“They may have done their job a particular way for a long time and might not be interested in changing or learning.
“As consumers we have to take our place in the process and make it clear that sustainability and retrofit are driving our buying decisions. If we use that buying power, they’ll soon come on board.
“You’ll end up with an energy efficient home that you understand because you helped to create it. You will have saved money and left a legacy.
“Another way I think the profession can really help is to discuss retrofit and its benefits with their customers when they’re already working on their properties, perhaps for a loft conversion or an extension. Because if you’re already spending tens of thousands on an extension, as we were, then suddenly an extra £23,000 to retrofit the rest of your house doesn’t seem so much.
“We looked for local installers and tried to find one that we didn’t feel was overselling us. We also wanted someone who was prepared to get to know the situation because it’s a quirky house and we are quirky people. They needed to understand that the environment was our major driver. Climate was first.
“If that meant giving up on a new sofa or something to get a better heat pump, then so be it.”
Writing the book
One hugely unexpected outcome of the project was how it’s led to a whole new life chapter for Judith, now author of a book that has so far sold 1,500 copies on Amazon.
“A lot of people were interested in what we had done and the savings we’ve made. They often said they’d love to do it themselves but wouldn’t have the time, money or knowledge. So I decided to write a book that is simple to understand, which I think is the benefit of it being written by someone like me, rather than a professional.
“I’ve interviewed the professionals and broken down the answers to my questions in a way that people can understand.”
The Social media phenomenon
Then came the social media stardom.
“I’d been doing the odd bit of social media, but when I did the Tedx Talk I started thinking I should get better at it. So I started posting the odd reel on Instagram, I filmed a dishwasher life hack and was sitting watching a movie when the notifications started coming through, bing, bing, bing, and it just went off like a rocket.
“I’m now doing a course on editing and learning about Pinterest and YouTube. I’m writing my blog and giving talks – I’m meant to be retired! The fact all this has happened has been the biggest surprise.
“I mean, whoever though that at 75 years old I was going to sit and talk about insulation and say, ‘wow, that was really interesting’.”
What’s next?
Far from finally putting their feet up, Judith and John have now embarked on a barn build for a home office in their garden. They’re hoping this will be completely self-sufficient with 10 solar panels and a storage battery which will also connect to the house.
They won’t be resting on the awareness-raising front either.
“I know how difficult it is to look the climate crisis in the eye and I’ll talk to anyone who listens about this,” Judith said.
“I managed my fear by going from eco worrier to warrior, looking at how I can make a difference.”
But what’s motivating them to keep going long after the dust has settled on their home retrofit?
“It’s creating a better life for our grandchildren,” Judith said. “My youngest grandson is seven and I have this image of him. I want him to die an old man in his bed surrounded by loved ones. I need to think I’ve done everything I could to provide them with a safe life.”
You can follow Judith’s barn journey, and get various environmentally-friendly life hacks on Instagram at @ecorenovationhome.
Have you completed an energy efficient building project or retrofit? We’d love to hear about it. Please get in touch by emailing news@renewableenergyinstaller.co.uk.
Image credit: Judith Leary-Joyce
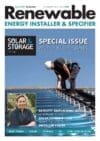